Scientists Have Invented a Method for Printing Metal Objects at Room Temperature
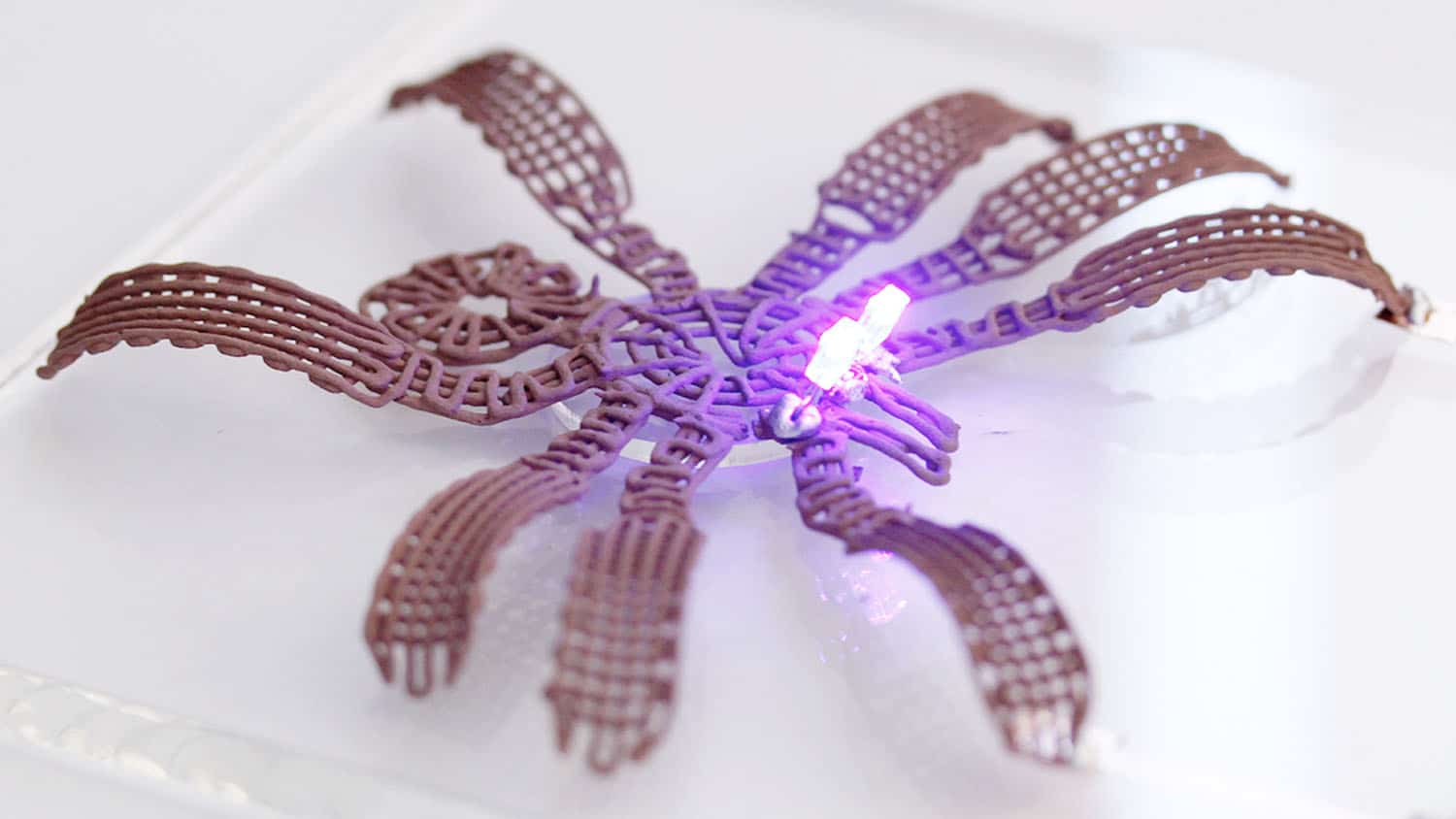
Existing methods of 3D printing metal objects require high temperatures, which makes it impossible to manufacture heat-sensitive components, including electronics. A group of scientists from the University of North Carolina has developed a new composition that allows for printing metal products at room temperature, according to New Atlas.
This new material is based on copper micro-particles dissolved in water. Micro-particles of the gallium-indium alloy (EGaIn), known as a eutectic alloy, as well as hydrochloric acid, are added to this solution. Hydrochloric acid lowers the pH of the water to 1.0, resulting in the removal of EGaIn oxides and the temporary transformation of the substance into liquid metal. The EGaIn droplets adhere to the solid copper particles and connect them together. The addition of methylcellulose to the mixture increases its volume.
"Since the printed objects are 97.5% made of metal, they have high conductivity. Obviously, this material is not as conductive as ordinary copper wire, but 3D printing copper wire at room temperature is impossible. And what we have developed is much more conductive than anything else that can be printed," says Michael Dickey, co-author of the article on this work and the Camille & Henry Dreyfus Professor of Chemical and Biomolecular Engineering at North Carolina State University.
.

The resulting viscous gel can be extruded through a nozzle of a regular 3D printer at room temperature, creating the product layer by layer. When the finished object dries at the same temperature, the water and hydrochloric acid evaporate. As a result, a rigid three-dimensional object with high electrical conductivity is obtained, which consists of 97.5% metal (the rest is methylcellulose).
"3D printing has revolutionized manufacturing, but there has not been a technology that allows for printing metal 3D objects at room temperature in a single step. This opens doors for a wide range of electronic components and devices. We are open to collaboration with industry partners to explore the potential applications of this technology and are always happy to discuss future research directions," says Professor Michael Dickey.
By controlling the gel extrusion and applying heat for rapid drying, the desired shape can be given to the object: a more complex detail can be obtained from a flat initial layer. In the video above, the gel was used to 3D print a spider that raises its legs when it dries under the influence of heating.